
- A couple of weeks ago AKF, the large Danish real estate developer, in partnership with Danish 3DCP Group, 3D printed a community building in greater Copenhagen area measuring 72 m2 (775 SF).
- The building will house a gym, guest room and common laundry facility for residents.
- Special low CO2 cement with 30% lower CO2 footprint was used in the concrete.
- Watch the video of the 3D construction printing process.
[Copenhagen, Denmark, December 12, 2023] – Concrete is widely known for its environmental impact and relatively high CO2 emissions during production. However, it is indispensable in construction for various reasons, including its unique properties such as price, strength and durability. With 3D printed concrete, many new opportunities are emerging to reduce the carbon footprint.
Thus, AKF, the real estate developer behind the building, stated the following in their press release: “3D printing is an adaptive construction process where material is added only where necessary. In the process, it is determined how much material should be used in different building components, making it possible to create buildings where concrete is only added where it is structurally necessary. This allows for a reduction in resource consumption and can bring significant environmental and economic benefits while providing greater freedom in the architectural design of the building”.
To further reduce the CO2 footprint, the entire AKF project was printed using low CO2 cement, which has a carbon footprint 30% lower than that of normal cement. The low CO2 cement was mixed with local sand and gravel and turned into 3D printable concrete using the D.fab admixtures method developed by Cemex and COBOD. Compared to 3D printing of mortars, the low CO2 cement 3D printable concrete reduces the CO2 footprint with 50%.
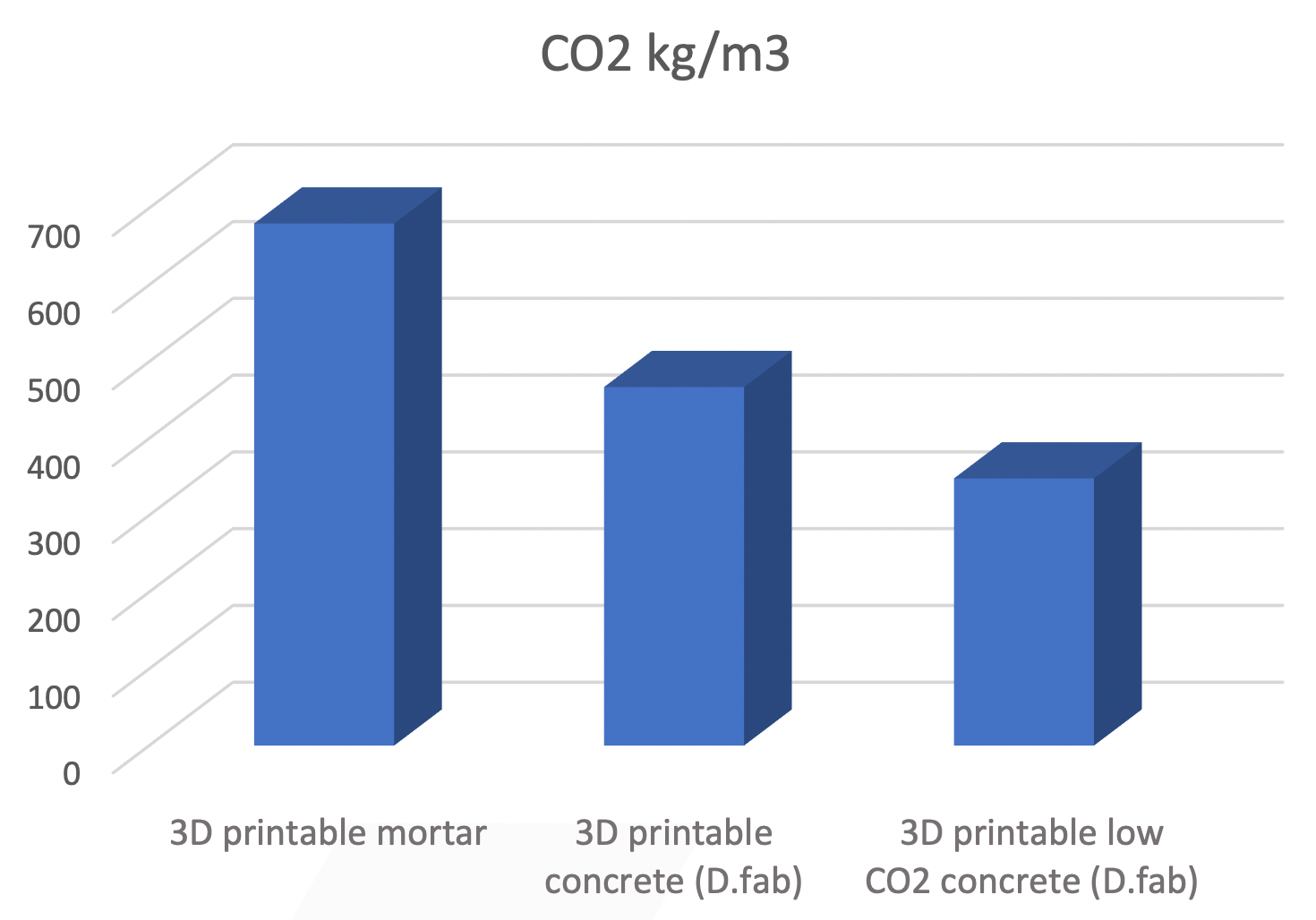
Generally, AKF sees significant potential in 3D printing technology that goes beyond concrete and envisions a future where natural resources like clay-rich soil can be used for 3D printed construction. Vibeke Lorenzen, the technical director at AKF, said: “3D printing opens the door to a world of possibilities, and hopefully, we can contribute to pushing the industry’s traditional construction methods”.
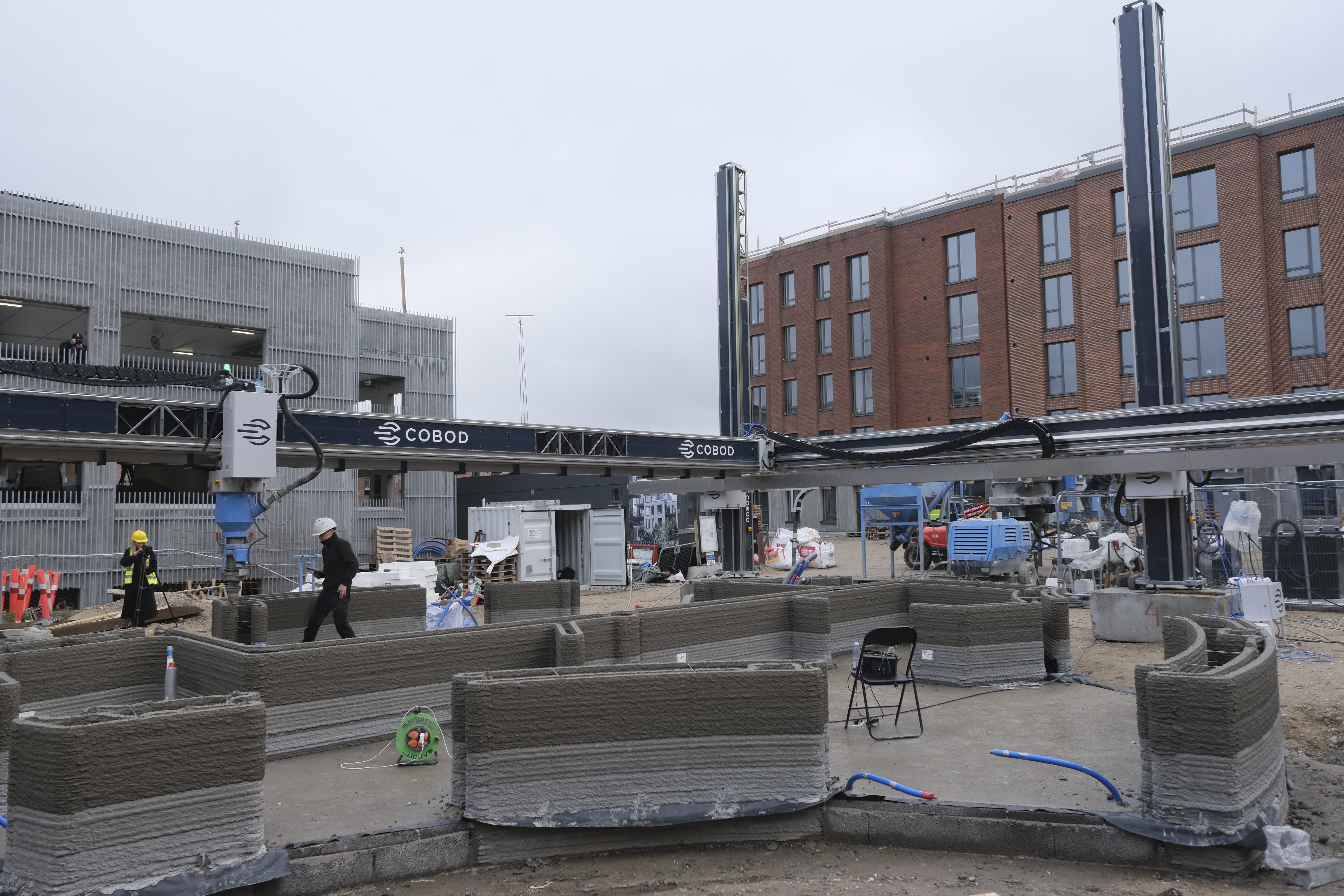
The whole community building was 3D printed using five printing days. During the printing there was a live PR event where the leading Danish news papers and construction magazines showed up to witness the printing process live. Mikkel Brich, CEO of 3DCP, explained: “Seeing is believing when it comes to new technology. So, we really wanted to show live how reliable, fast and precise the technology is and we are really happy for the turnout from the press, that came in large numbers”.
The finished community building will be 72 m2 (775 SF) and contain a gym, a guest room and common laundry facility for the residents of the surrounding apartment buildings.
Saga Architects who also designed the first building 3DCP Group made in Denmark, the tiny house in Hobro, strived to make the community building appear even more forthcoming and friendly by using a lot of wood for the decorative parts and organic shapes for the walls, a detail virtually impossible to make with conventional methods.
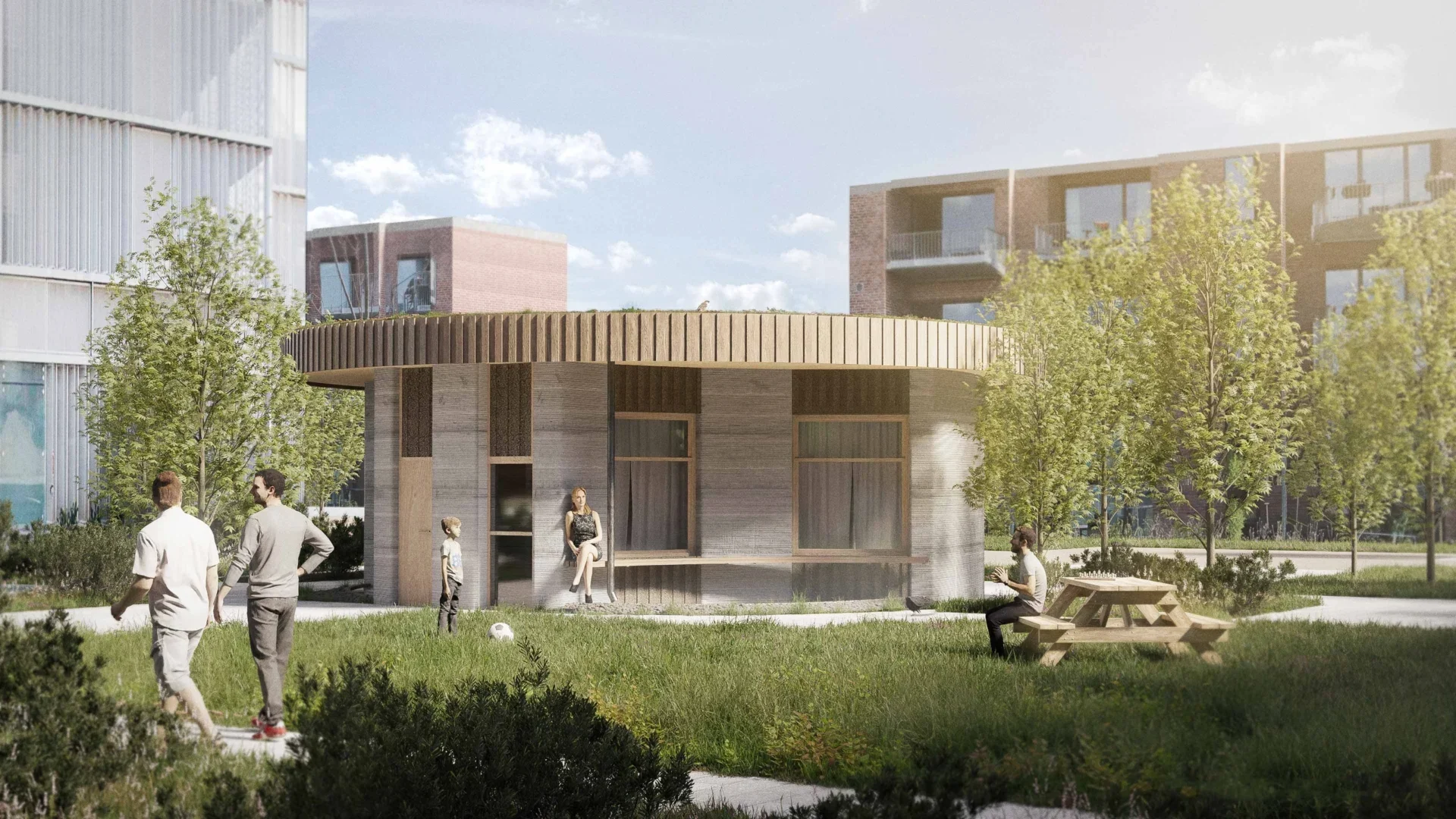
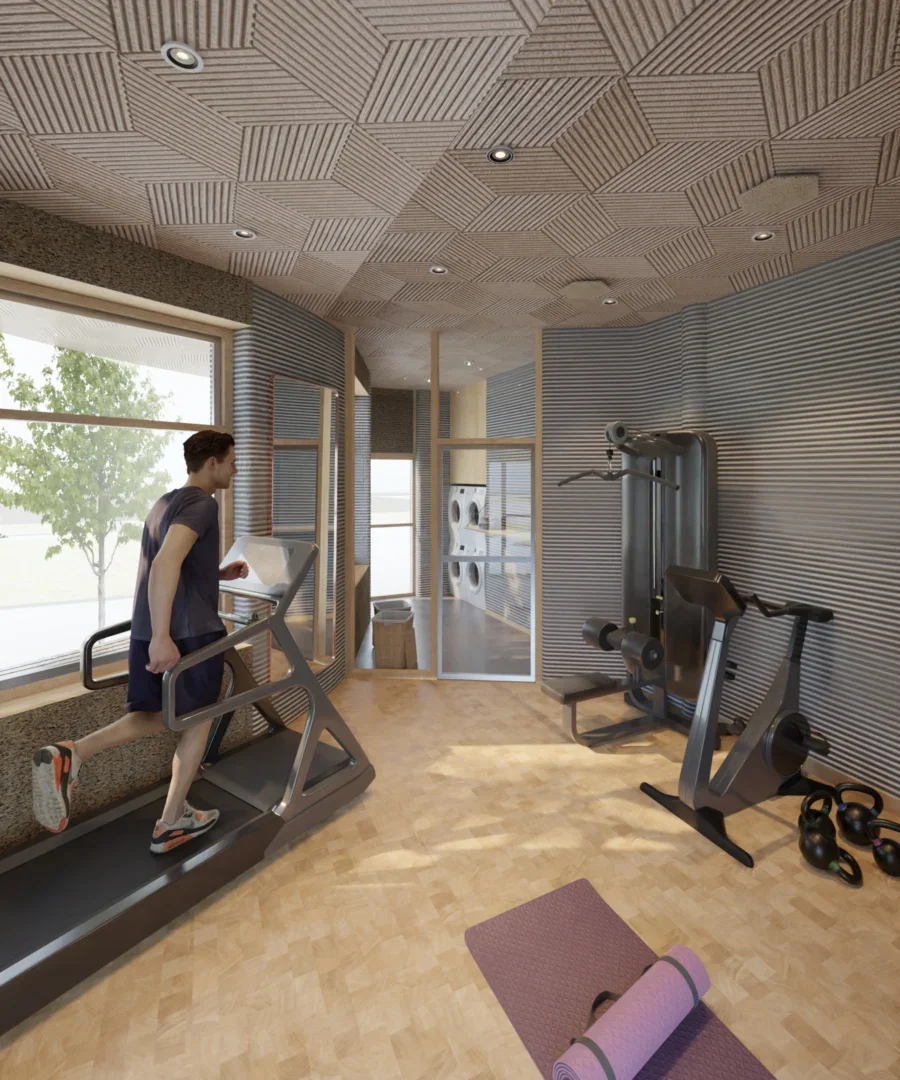
RELEVANT LINKS:
- COBOD International website
- 3DCP Group website
- SAGA Space Architects website
- AKF website
- Video of the printing
ABOUT COBOD INTERNATIONAL
COBOD stands as the global leader in supplying 3D printers for the construction sector, promoting over 70 printers distributed across North and Latin America, Europe, the Middle East, Africa, and Asia-Pacific. Driven by a mission to revolutionize construction through multifunctional robots utilizing 3D printing, COBOD envisions automating half of the construction processes to achieve faster, cost-effective, sustainable results with enhanced design versatility.
From residential, commercial, and public structures to sports facilities and educational institutions, COBOD’s 3D printers have been instrumental in erecting 1 to 3-story structures across all six inhabited continents. Their innovative technology also extends to developing large-scale data centers, wind turbine towers, and more.
Embracing an open-source material approach, COBOD collaborates with global partners, including customers, academia, and suppliers. The company, backed by prominent shareholders such as General Electric, CEMEX, Holcim, and PERI, operates from its main office in Copenhagen, Denmark, and regional competence centers in Miami, Florida, and Kuala Lumpur, Malaysia. COBOD’s dynamic team comprises over 100 professionals from 25 diverse nationalities.
ABOUT 3DCP GROUP
3DCP Group consists of an engineering company, architecture firm, and the constructing party, which combined possess all the skills necessary to 3D print a complete building.
This gives 3DCP a unique opportunity to take care of the entire construction process, from idea to turn-key product.
3DCP’s ambition is to build better, cheaper, and more sustainably.
When the company says its ambition is to build better, it doesn’t just mean the objective quality of the house, but also the subjective experience of the house – all of which is made possible through the construction method and the surrounding processes.