Meeting the global demand for affordable housing is a significant challenge. This article examines how 3D construction printing (3DCP) can be effectively applied to residential and social housing projects. By looking at real-world examples, it highlights the benefits of 3DCP, including faster construction times, cost-efficiency, and design flexibility.
Why should 3D Construction Printing be used?
Affordable housing is a human right, yet a UN report indicates that 1.6 billion people worldwide lack it. This figure is expected to increase to 3 billion within the next six years, emphasizing the urgent need to provide affordable homes. To address this crisis, UN-Habitat estimates that 96,000 new affordable homes need to be built daily until 2030. This challenge is not only about numbers but also a race against time, putting pressure on the construction industry to increase productivity while reducing costs. Traditional construction methods are considered insufficient in achieving this ambitious goal. However, one viable solution is 3D construction printing (3DCP), as suggested by World Economic Forum, and we agree. This technology offers an efficient and cost-effective alternative to traditional construction methods, making it possible to build residential homes and social housing projects more quickly and at a competitive cost.
Residential Construction & Social Housing Projects
Both residential construction and social housing projects aim to create homes where people feel safe and comfortable. While project size may differ, the need for affordability, shorter construction times, and design flexibility is paramount in both areas. 3DCP meets these needs by allowing for customization and efficient construction.
Family Home in Portugal
In February 2024, Havelar, a COBOD customer in Portugal, completed the country’s first 3D printed home. This two-bedroom house, measuring 80 m² (861 SF), was finished in just two months – eight times faster than traditional construction methods in Portugal. The walls were printed in only 18 hours, showcasing the speed and efficiency of 3DCP.
In addition to the expedited construction timeline, 3D printed homes offer cost-effective solutions. “With €150,000, it’s possible for a young couple to have the home they’ve always dreamed of, in an area with good access and services“, says Havelar Co-Founder Rodrigo Vilas-Boas. This affordability is achievable due to the reduced construction timeline, efficient material usage, and a smaller construction team. The technology also allows for quick customization, adapting the base house model to specific homeowner needs without significant delays or further costs.
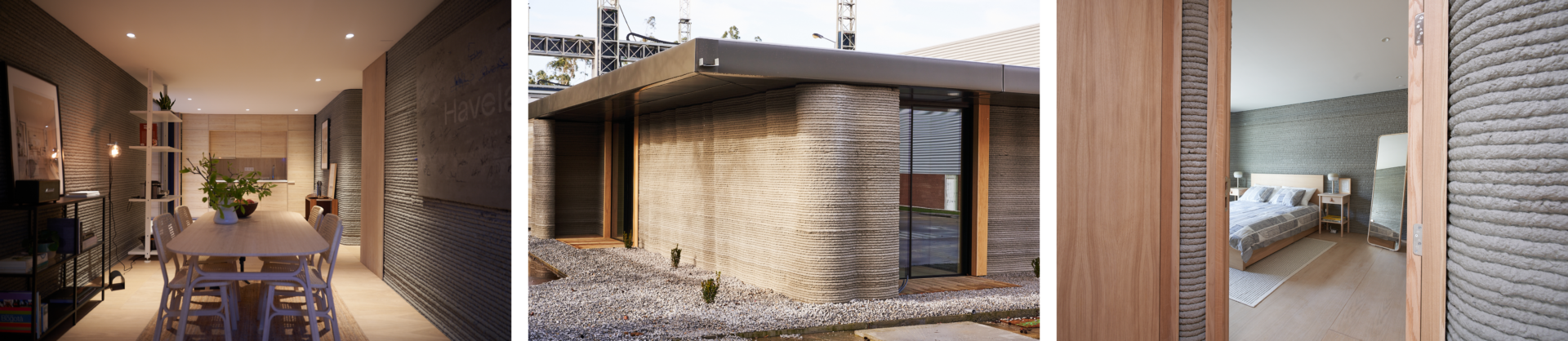
Luxury Villa in Saudi Arabia
In 2022, a three-story, 345 m² (3,713 SF) villa in Saudi Arabia was printed in just 26 days by our customer Dar Al Arkan. The project used local raw materials in combination with the D.fab additive solution co-developed by Cemex and COBOD, achieving a material cost of less than a total of €10,000 for the printed part of the structure. This demonstrates the cost-effectiveness of 3DCP. The ability to adjust the dimensions of the 3D printer was also vital for constructing the large luxury villa, illustrating the scalability of 3D construction printing.
Wael al Hagan, former Project Manager at Dar Al Arkan, stated: “The introduction of 3D construction printing enables us to focus on greater design flexibility, strengthen productivity, and achieve higher cost efficiency.“
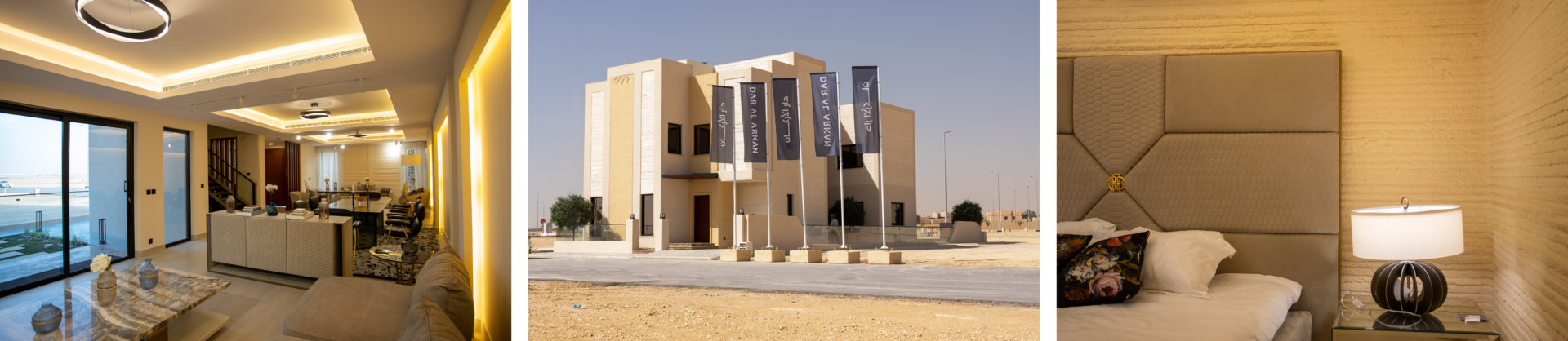
Wildfire Restoration Home
In Redding, California, our customer Emergent3D built a 110 m² (1,200 SF) home designed for families who lost their homes to wildfires. The structure is more resilient to wildfires because it is printed with high durability concrete and adheres to California’s building codes. The material cost for the 3D concrete printed walls was less than USD 5,000 for the printed structure and the printing process took just 30 hours. The 3D construction technology allowed for unique, undulating, organic wall shapes and floor-to-ceiling windows envisioned by the architect Benjamin Albertson, resulting in a stunning design.
The area around Redding was severely affected by wildfires in 2018, with more than 1,500 homes lost. Emergent3D views 3D construction printing as a long-term solution for rebuilding homes that are more resilient to natural catastrophes. The plan is to replicate this design numerous times, providing durable and comfortable housing for families impacted by wildfires.
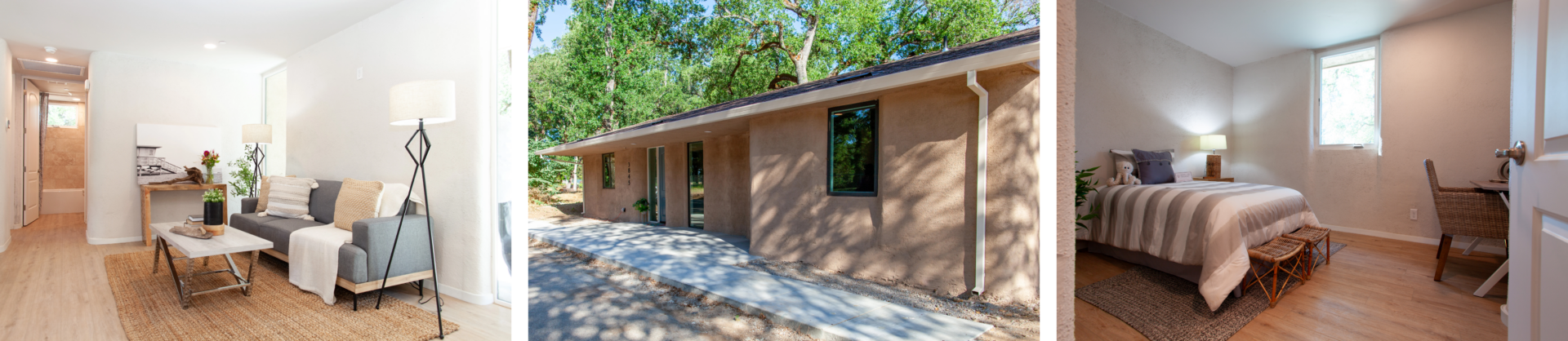
Conclusion
3DCP is a relatively new innovative technology that through automation, shortens construction time and reduces overall project costs. The design and material flexibility allow the customization of projects to individual needs but also environmental conditions, making it ideal for residential and social housing projects all around the world.
3DCP already demonstrates significant potential for more effective and efficient construction methods. As technology advances, its benefits are expected to become even more pronounced, as also suggested by the World Economic Forum. 3DCP involves a learning curve for the ones new to the technology, where each project brings new learnings and insights that enhance productivity for future ones. This iterative learning process ensures that the efficiency and effectiveness of 3D construction printing will continue to improve over time and should be considered part of the solution to the affordable housing crisis.